Descrizione
Il progetto consiste in una piastra riscaldante per saldare e dissaldare componenti su circuiti stampati. Include sensori NTC per misurare la temperatura della piastra, un convertitore analogico-digitale con amplificatore programmabile, e un microcontrollore ESP32. Quest’ultimo gestisce dei riscaldatori ceramici con un algoritmo software PID.
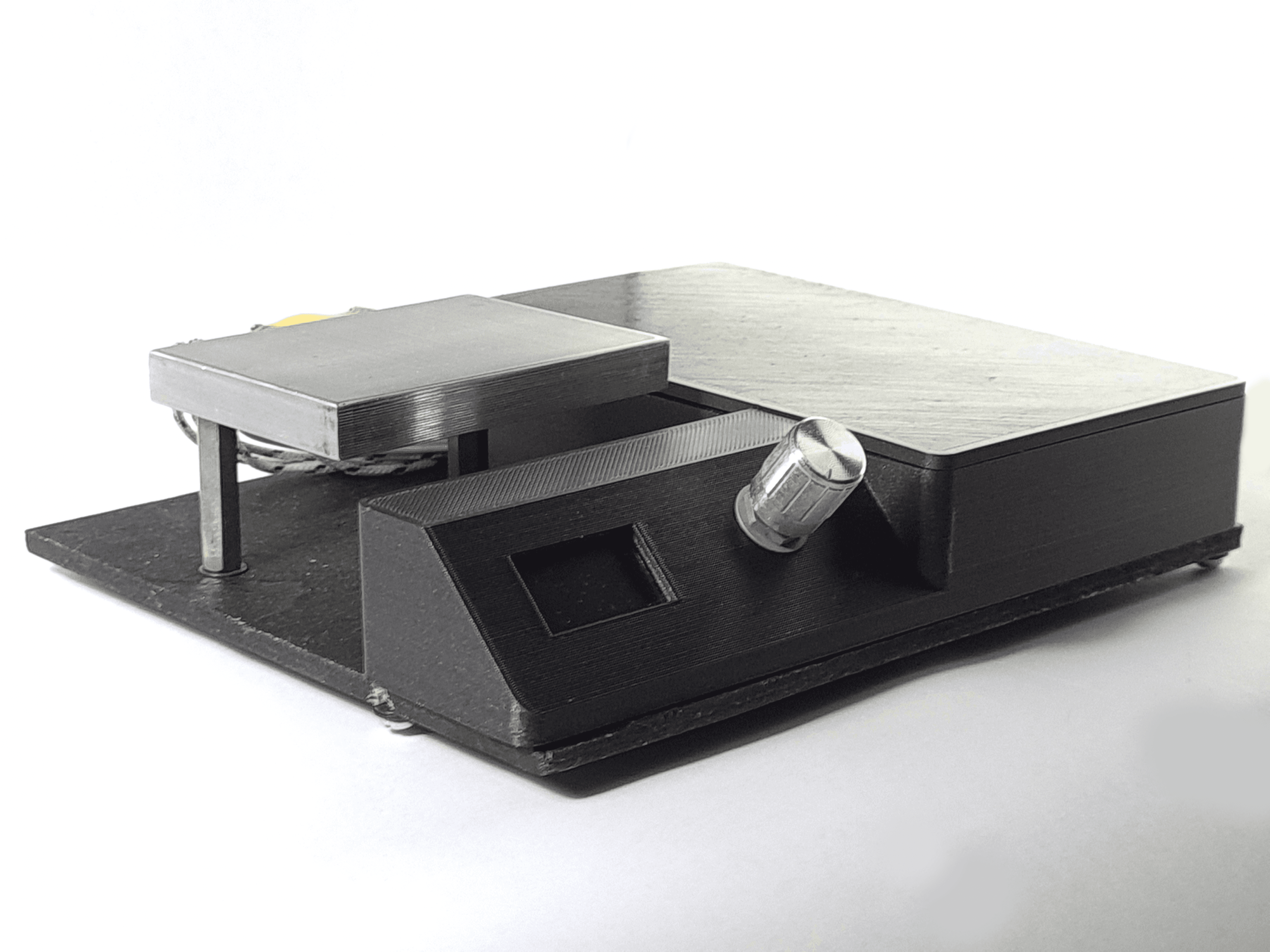
Componenti del dispositivo
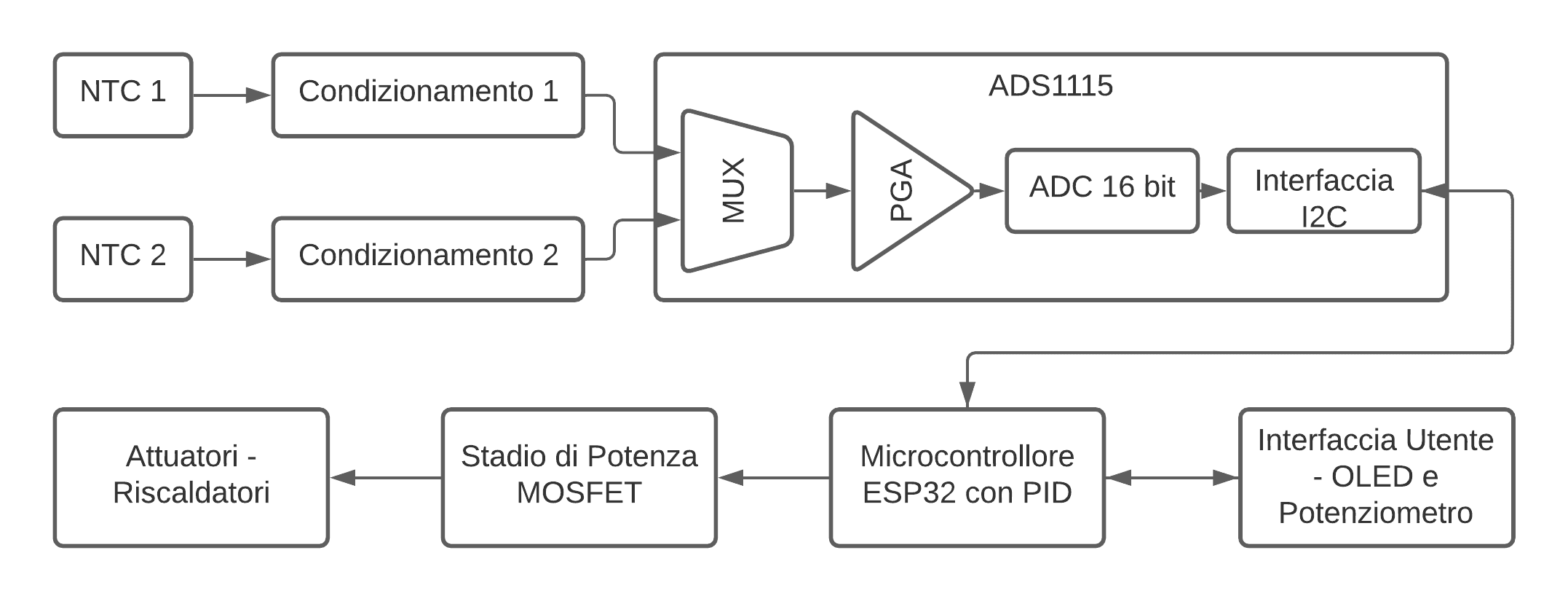
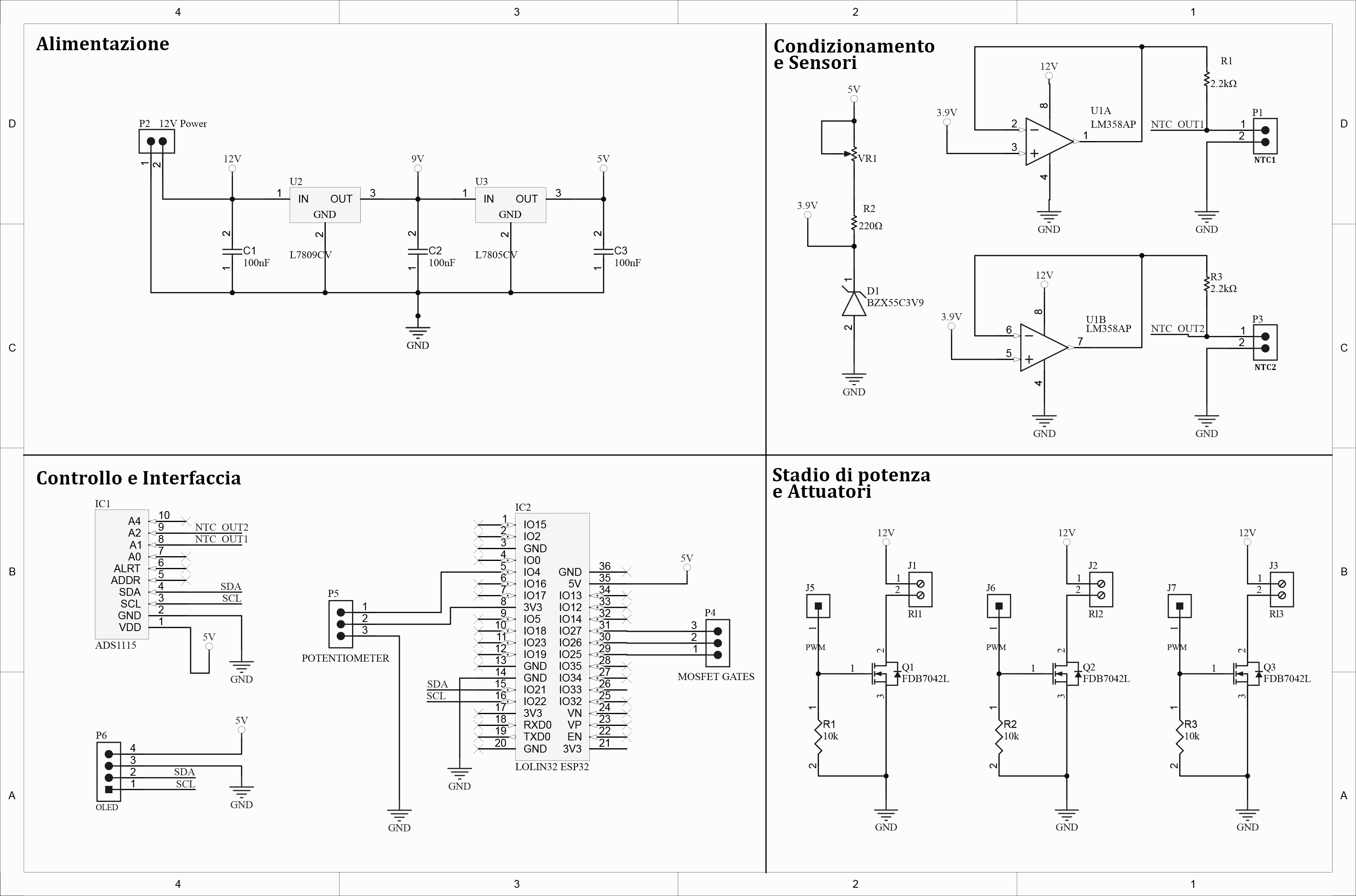
Trasduttore di temperatura
Il dispositivo utilizza due termistori NTC (Negative Temperature Coefficient), sensori di temperatura a semiconduttore drogato con una caratteristica decrescente: all’aumentare della temperatura, la resistenza diminuisce. Poiché l'andamento è non lineare, è necessaria una linearizzazione della caratteristica ingresso-uscita.
Riferimento di Tensione
Il riferimento di tensione di 3.9V alimenta il sensore di temperatura mantenendo stabile la tensione a fronte di possibili variazioni dovute alla temperatura o al carico. È composta da una serie di resistore, trimmer e diodo zener BZX55-3.9V. Con il trimmer è possibile regolare finemente la corrente che attraversa il diodo, che ha una caduta di tensione precisa. Questa tensione viene poi disaccoppiata dal circuito successivo composto da un amplificatore operazionale LM358 in configurazione buffer.
Linearizzazione dell’NTC
Per linearizzare il termistore NTC, bisogna conoscere alcuni parametri per determinare il valore del resistore di linearizzazione da mettere in serie. In particolare, è necessario conoscere la costante β, che in questo caso è 3950K, e la resistenza ad una temperatura di riferimento, che risulta essere 100kΩ a 25 °C. Come ultimo passaggio, bisogna scegliere un intervallo di temperatura misurabile dal sensore, che in questo caso va da 0 °C a 260 °C, con una temperatura media di 130 °C.
Per determinare la resistenza dell'NTC a una determinata temperatura , si utilizza l'equazione:
dove è la resistenza dell'NTC alla temperatura , e è la temperatura di riferimento.
Essendo la caratteristica I-U dell'NTC non lineare, si introduce una resistenza di linearizzazione , calcolata con la formula:
Questa resistenza viene inserita in serie al termistore, e la tensione ai capi dell'NTC si ottiene con:
In questo modo si ottiene una caratteristica più lineare per l'NTC.
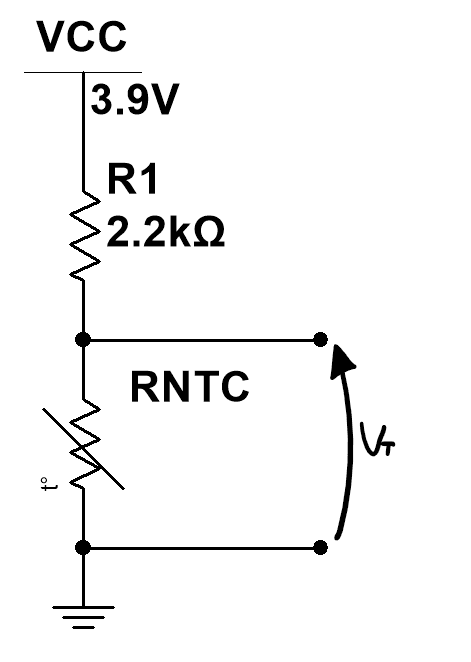
Acquisizione dati
Il blocco di acquisizione è rappresentato da un ADC (Analog-to-Digital Converter) ADS1115 della Texas Instruments, che offre una risoluzione a 15 bit su un intervallo di tensioni positivo tra 0V e 4.096V. Grazie a questa risoluzione, l'ADC permette di ottenere una misura precisa della caduta di tensione ai capi dell'NTC, che può essere al più 3.9V. Quindi in questo caso il guadagno dell'ADS1115 è impostato su 1, rendendo il dispositivo compatibile con l’intervallo di tensioni dei sensori. L'ADC comunica il valore misurato all'ESP32 tramite l’nterfaccia I2C, e il microcontrollore effettua i calcoli per associare il valore di tensione ad una determinata temperatura.
Microcontrollore ESP32
L’ESP32-WROOM-32 è stato scelto per le sue caratteristiche avanzate: 4MB di memoria flash, 34 pin I/O, ADC a 12 bit, DAC, connettività Bluetooth e Wi-Fi. Nello specifico, si occupa della elaborazione dati e la gestione degli altri componenti: interfaccia utente, sensori, blocco acquisizione dati, stadio di potenza. Per quanto riguarda l’elaborazione, i dati ricevuti dal blocco di acquisizione, vengono elaborati con un algoritmo software PID, che gestisce impone un segnale PWM variabile allo stadio di potenza a cui sono collegati i riscaldatori ceramici.
Interfaccia utente
L'interfaccia utente include un potenziometro per impostare la temperatura desiderata e un display OLED da 0.96 pollici. Questo mostra la temperatura rilevata dai singoli sensori, quella media e quella impostata.
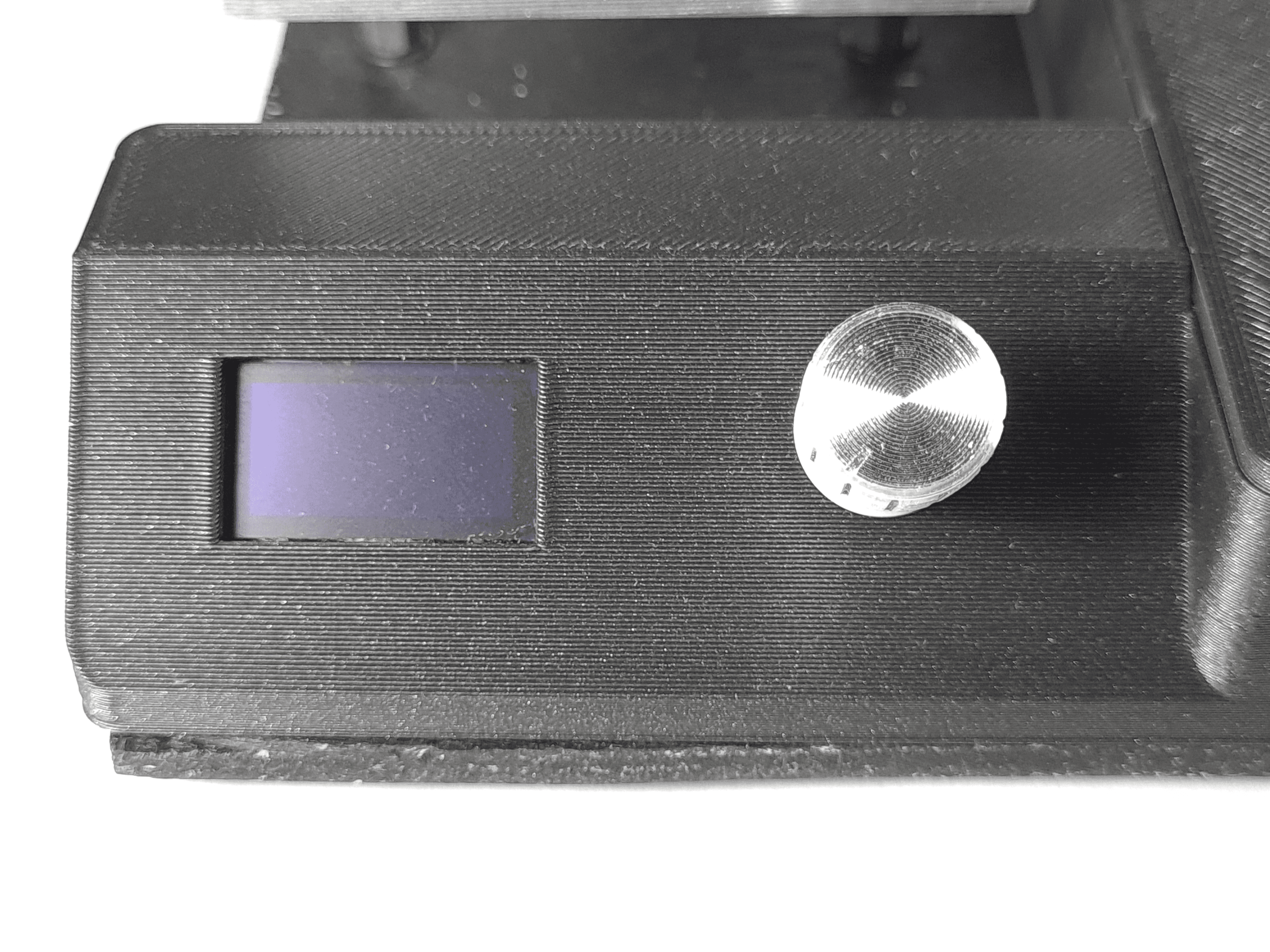
Stadio di potenza
Lo stadio di potenza utilizza tre MOSFET ad enhancement a canale N modello FDB7042L, che sono stati recuperati da una scheda madre per PC. Hanno un formato SMD, e sono adatti per essere controllati a basse tensioni gate-source. Praticamente sono ideali per un microcontrollore come l'ESP32, che funziona a 3.3V. Il circuito, che gestisce i riscaldatori, è progettato affinché i MOSFET operino nelle tre zone di funzionamento: triodica, saturazione e interdizione.
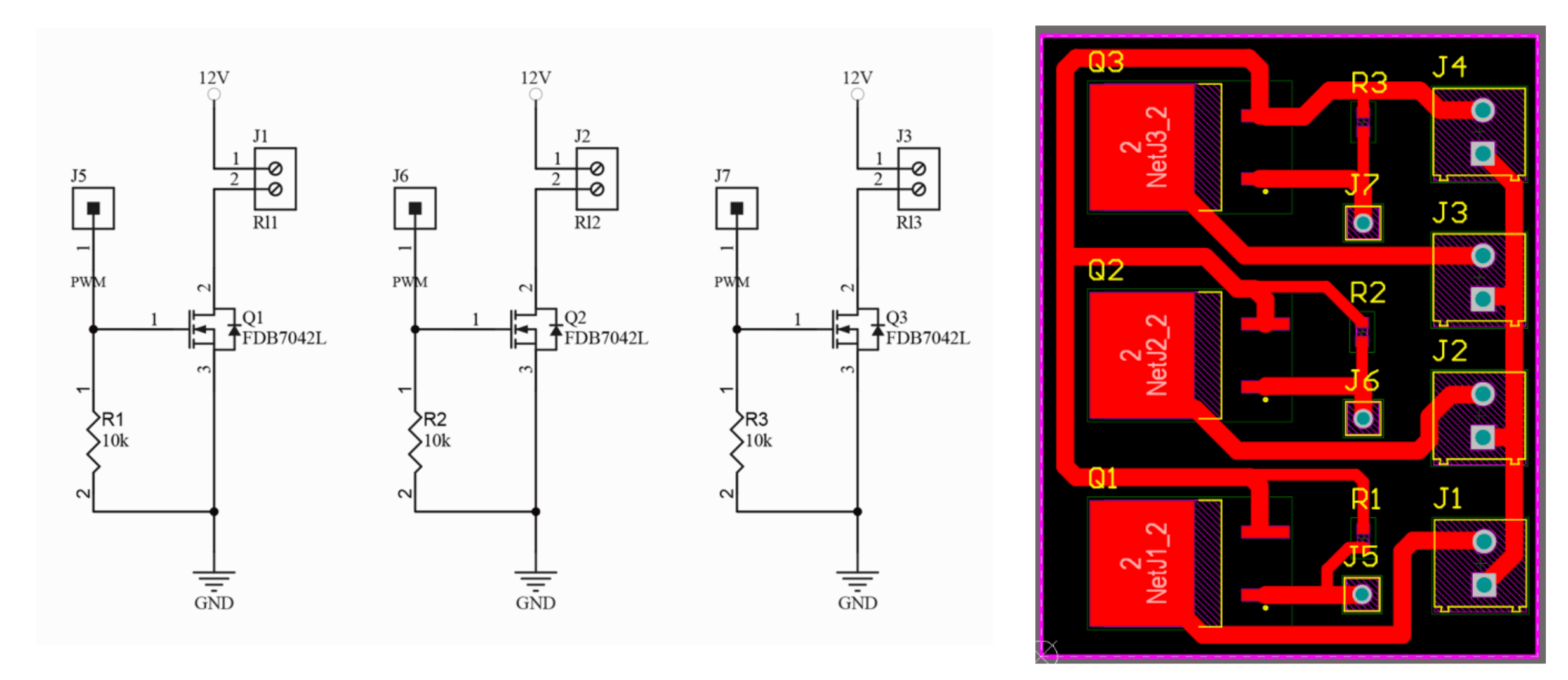
Realizzazione Pratica
Il circuito di controllo e di potenza sono stati realizzati su circuiti stampati separati. Il PCB è stato realizzato con Altium Designer, a partire dallo schema elettrico, per poi creare al PCB. Successivamente, dopo la preparazione dei fie su FlatCAM, sino stati fresati con una CNC. Il risultato finale con i componenti montati sono presenti nelle immagini a seguire. La scheda di controllo contiene il condizionamento dei sensori, il blocco di acquisizione e il microcontrollore. Mentre la scheda del circuito di potenza è formata dai tre MOSFET a canale N, a cui sono collegati i tre riscaldatori ceramici.
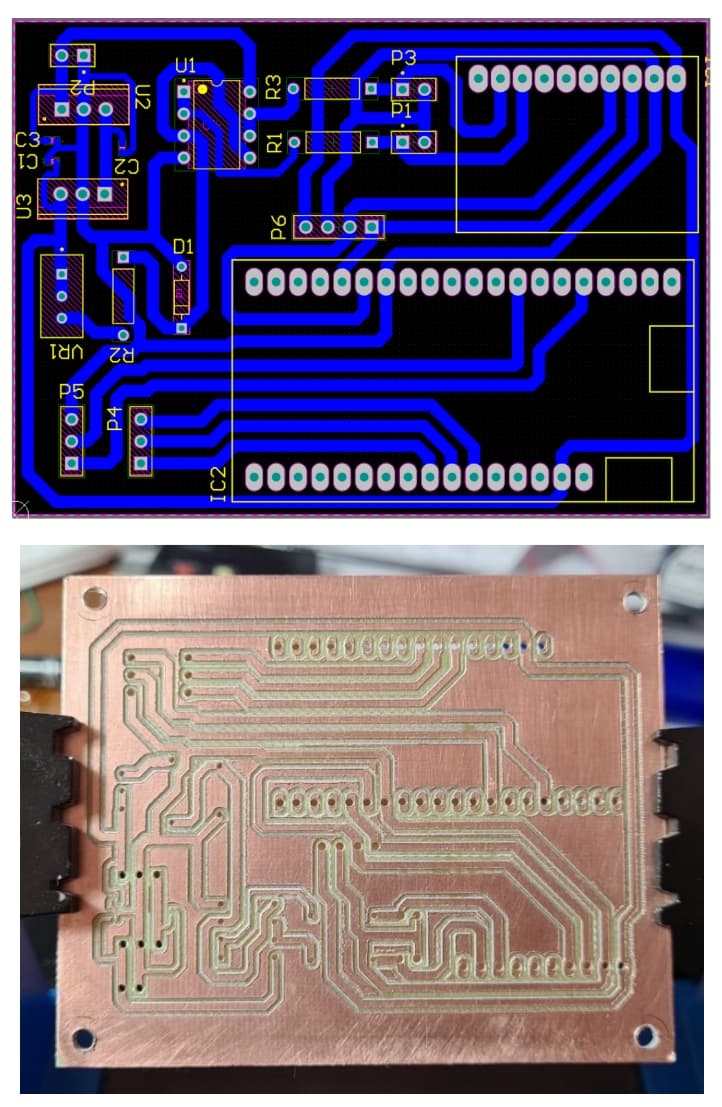
Struttura meccanica
La struttura meccanica del progetto è costituita da un blocco in alluminio, lavorato e forato per alloggiare tre riscaldatori e due sensori NTC. Il blocco è montato su una base di compensato con distanziatori per isolarlo dalle parti sensibili. La figura seguente mostra il disegno 3D realizzato in Fusion 360.
Inoltre, è stato modellato anche un contenitore stampato in 3D, per contenere tutta la parte di elettronica, rendere il progetto più professionale e sicuro. È presente anche un coperchio removibile per accedere all'elettronica interna.
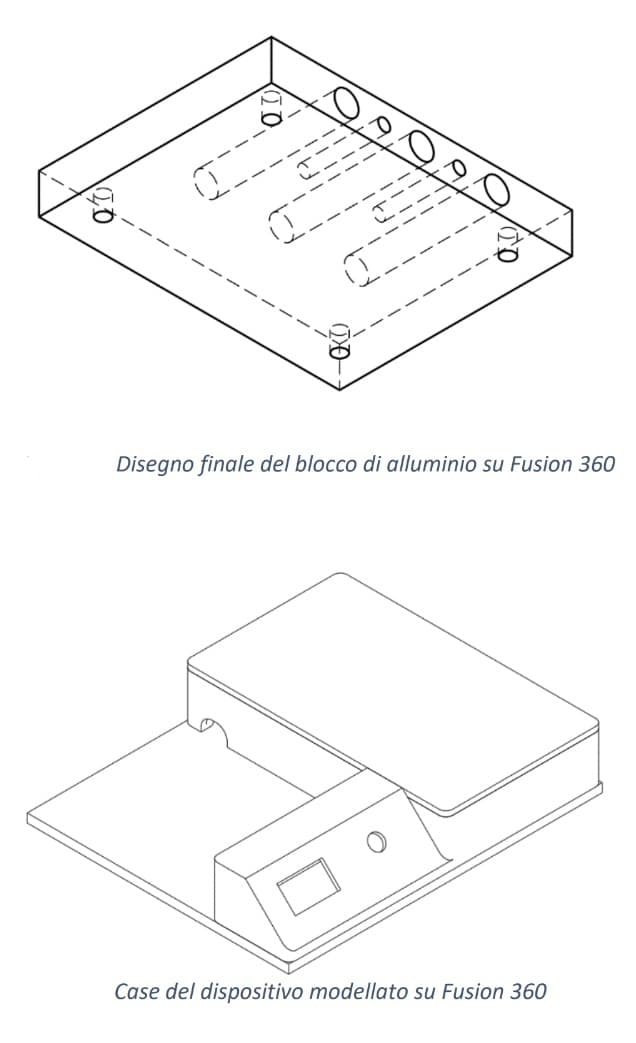
Sistema di controllo PID
Il sistema di controllo del progetto utilizza un regolatore PID implementato a livello software. Questo è applicato in un sistema retroazionato dove l'errore, cioè la differenza tra il valore impostato dal potenziometro (da 0°C a 260°C) e la temperatura rilevata dagli NTC, è fondamentale. Il PID calcola la variabile di controllo che genera un segnale PWM variabile da 0 a 255 bit, regolando i transistor che gestiscono la potenza trasmessa ai riscaldatori.
Il PID si compone di tre regolatori:
- Proporzionale (P): genera un'uscita proporzionale all'errore.
- Integrale (I): produce un'uscita proporzionale all'integrale dell'errore.
- Derivativo (D): restituisce un'uscita proporzionale alla derivata dell'errore.
Questi regolatori permettono al sistema di raggiungere la temperatura desiderata, senza oscillazioni al valore di regime come nel controllo ON-OFF.
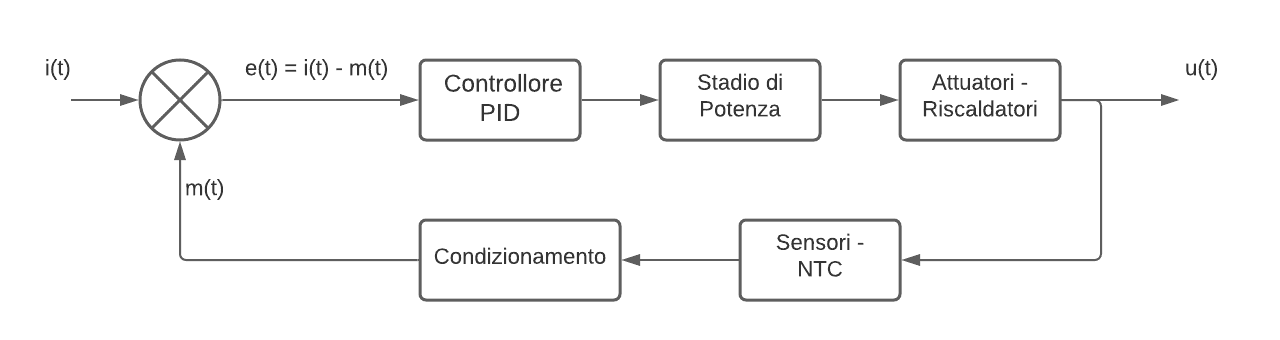
Risultati
Il grafico in figura mostra la risposta del controllo PID a un impulso, con il potenziometro impostato a un massimo di 250°C. Le costanti PID sono: Kp = 25, Kd = 5, Ki = 0.5. Attraverso vari test, si ottiene la curva blu che rappresenta l'uscita u(t) del sistema.
Le costanti sono state determinate attivando i singoli regolatori. Prima è stata applicata la costante Kp, che provoca un errore a regime costante. Successivamente è stato aggiunto il blocco derivatore, che non ha un impatto significativo durante il transitorio. La costante del blocco integratore è bassa, poiché causa sovraelongazioni oltre 10°C rispetto al valore impostato. Per mitigare questo, si è stabilita una condizione che attiva l’integratore solo quando l'errore è prossimo a zero. Questo ha portato a una sottoelongazione di pochi gradi. Infine, grazie al contributo del blocco integratore, l'errore a regime è praticamente nullo, con variazioni minime di ±0.5°C. La figura seguente mostra la risposta in dettaglio.
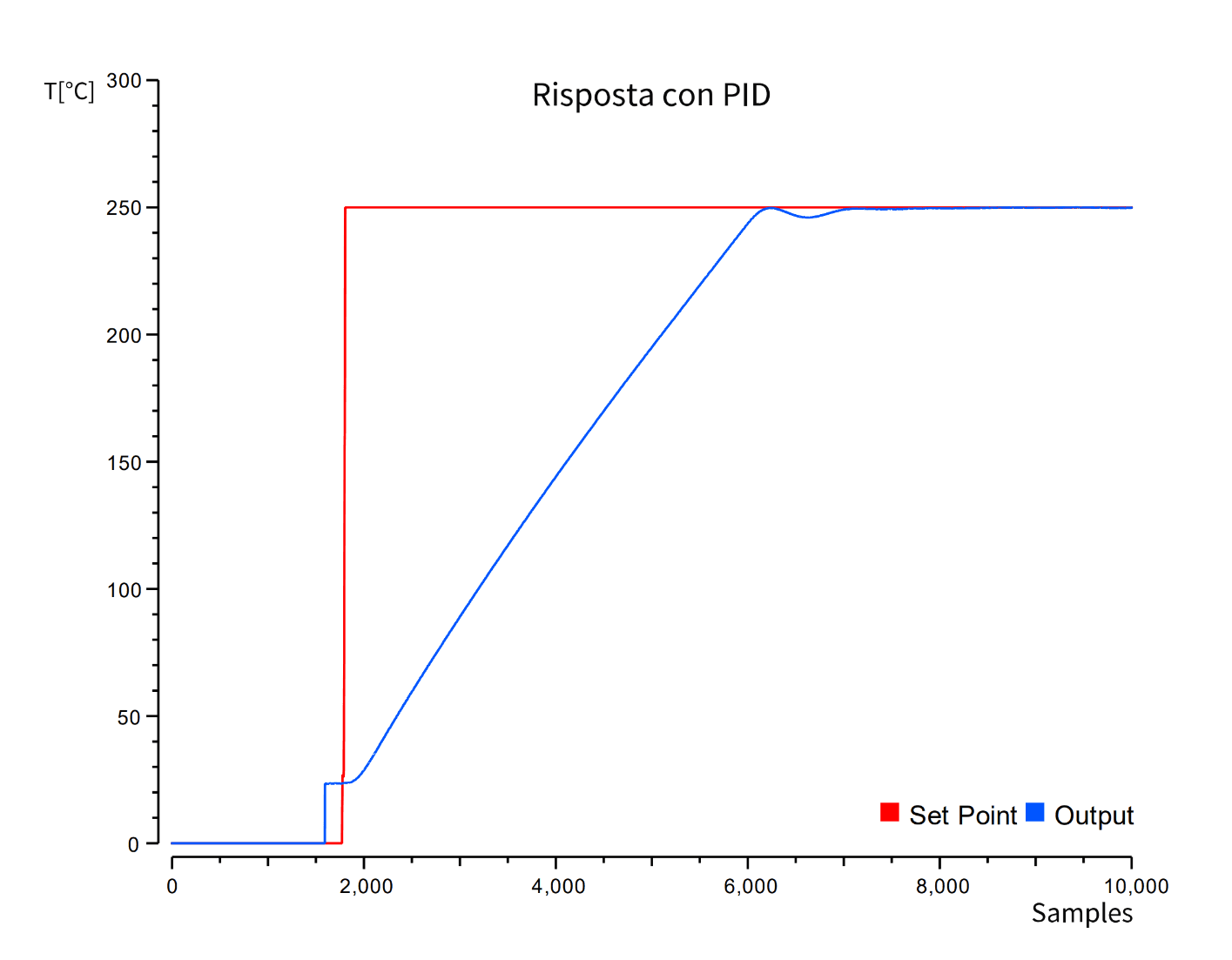
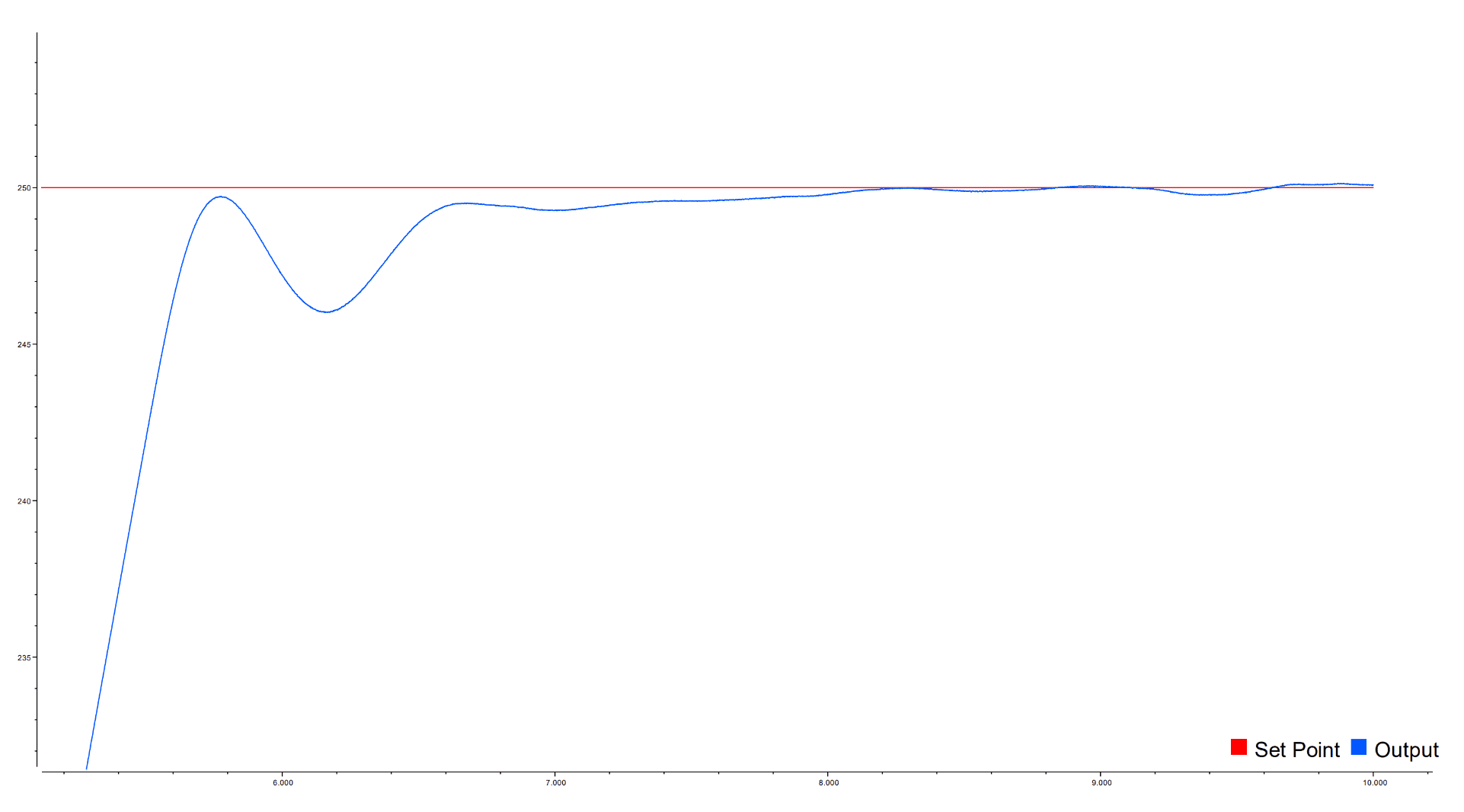
Conclusioni
Il progetto ha raggiunto l'obiettivo di saldare e recuperare componenti preziosi su circuiti stampati, riuscendo a sciogliere lo stagno a diverse temperature. Mentre il processo di saldatura è altrettanto semplice: si applica la pasta saldante sull'impronta del componente, si posiziona il componente e si avvia la piastra riscaldante, garantendo una saldatura di qualità superiore rispetto a quella manuale.
Tuttavia, ci sono margini di miglioramento. Attualmente, la temperatura è impostata tramite un potenziometro; un possibile miglioramento da fare è sviluppare un interfaccia per selezionare profili di temperatura specifici.
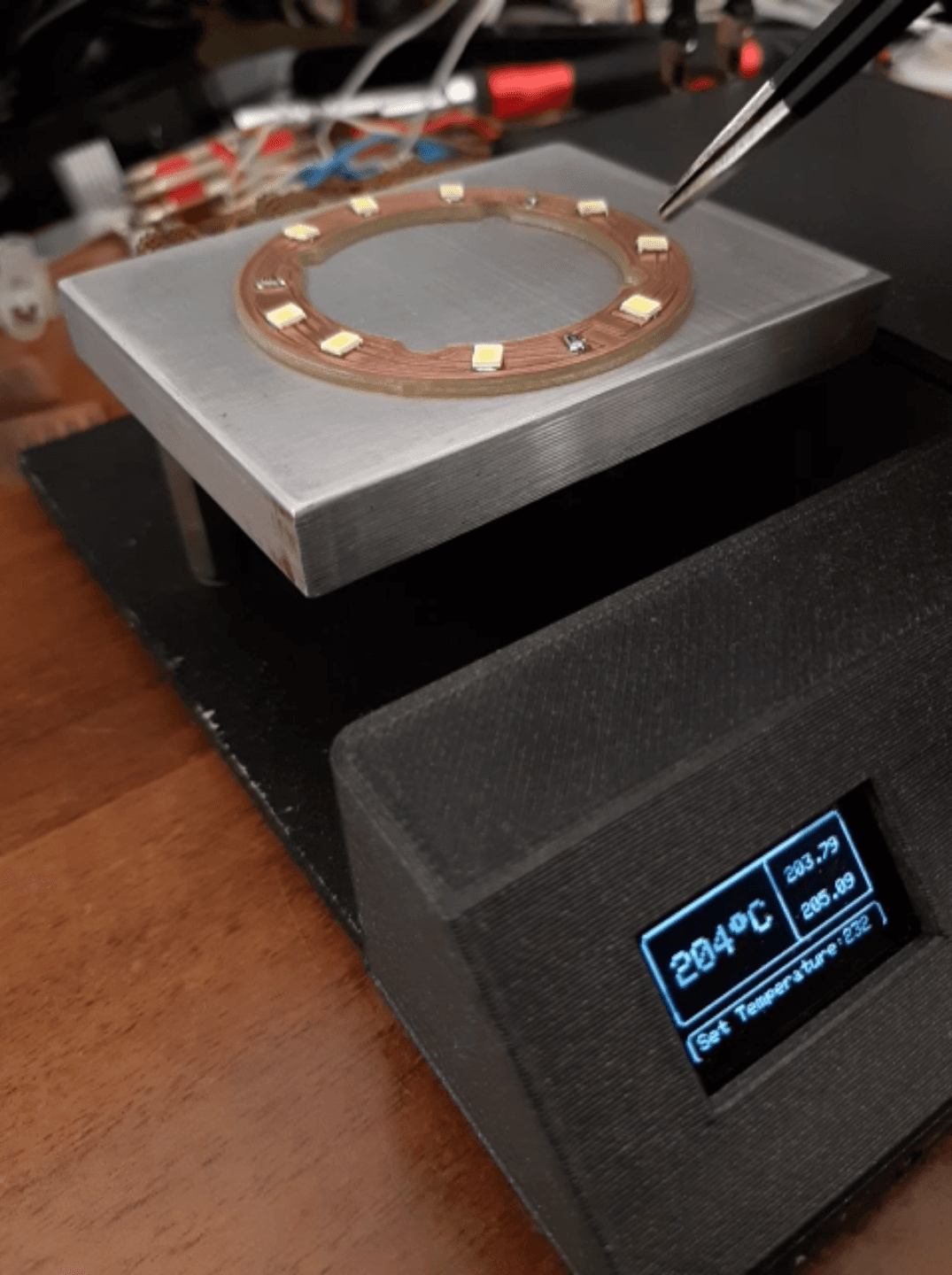